a new project 'forced' me to get some new tooling.
This piece of 4140 1/2" diameter annealed round bar
will be used to make a boring bar. first the machining,
then heat treating, and finally a clean up.
This piece of 1018 1-1/2" hot rolled bar stock
will be used for a v block.
This 1/2" solid carbide end mill is touted for use with
aluminum. so far i have been using HSS only on aluminum.
The surfaces are not coated and polished to point of being
a mirror finish so sticking should be minimal.
This nice little 1/4" square broach will be used to finish the
square hole in the boring bar. I could have bought a few boring
bars for the price of this broach but I watched Adam on ABOM79
use a 2" broach to make a keyway and I wanted to try one out.
Here is a low cost 3" indexed facing mill. Looking through MSC
these things cost upwards of $600, this little gem was $150 on
Amazon. Accusize imports tools from all over the world including
:chinese:. It isn't clear where this mill was made but I can't believe
it came from a US manufacturer for the price. I also ordered, but
did not receive yet inserts for aluminum. The inserts that came with
it are for ferrous metals.
So the first project is to turn the 1-1/2" hot rolled bar stock into v blocks,
I actually have two pieces of this size steel, so two v blocks. The center
of each v block will have a 1/2" hole drilled to allow passage of the 1/4"
square broach as it gets pressed through the pilot hole of the 1/2" diam
4140 round bar stock that will end up being a boring bar for general
removal and threading.
:thumbsup:
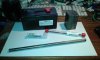
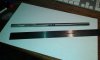
This piece of 4140 1/2" diameter annealed round bar
will be used to make a boring bar. first the machining,
then heat treating, and finally a clean up.
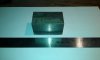
This piece of 1018 1-1/2" hot rolled bar stock
will be used for a v block.
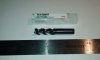
This 1/2" solid carbide end mill is touted for use with
aluminum. so far i have been using HSS only on aluminum.
The surfaces are not coated and polished to point of being
a mirror finish so sticking should be minimal.
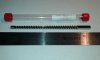
This nice little 1/4" square broach will be used to finish the
square hole in the boring bar. I could have bought a few boring
bars for the price of this broach but I watched Adam on ABOM79
use a 2" broach to make a keyway and I wanted to try one out.
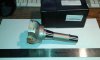
Here is a low cost 3" indexed facing mill. Looking through MSC
these things cost upwards of $600, this little gem was $150 on
Amazon. Accusize imports tools from all over the world including
:chinese:. It isn't clear where this mill was made but I can't believe
it came from a US manufacturer for the price. I also ordered, but
did not receive yet inserts for aluminum. The inserts that came with
it are for ferrous metals.
So the first project is to turn the 1-1/2" hot rolled bar stock into v blocks,
I actually have two pieces of this size steel, so two v blocks. The center
of each v block will have a 1/2" hole drilled to allow passage of the 1/4"
square broach as it gets pressed through the pilot hole of the 1/2" diam
4140 round bar stock that will end up being a boring bar for general
removal and threading.
:thumbsup:
Last edited: