Hi, I'm new to the forum and though I've been building motorcycles for many years, I've never had a CVT-equipped bike. Well, that's finally changing. Since my knowledge of industrial engines and torque converters is less than diddly, I've recently spent a bunch of hours online, educating myself on mini-bike/go-kart tuning and fabrication. More often then not, the most useful search results led me to this forum, so I figured I should register and jump head-first into the very deep rabbit hole of Predator/GX performance. There are lot of very knowledgeable people here, building some very cool little machines!
I have a fairly well-equipped shop, but its quite compact, and I recently found my parts shelves running out of space. So, I decided to take a pile of very random cast-off parts from various motorcycle projects and see how cheaply and easily I could build a bike out of them. For my framework, I bought a salvage frame from a '74 SST/Panther 175 Black Shadow for under $100 off Ebay. I started hanging parts off it with a vauge idea of building a street-legal gravel runner for exploring the flat, unpaved farm roads of rural Kansas.
Originally, I was thinking that a Yamaha Blaster 200 motor would go nicely in this frame, but that turned out to be a more expensive proposition than I had expected. Meanwhile, a friend of mine recently helped build a KX/Predator 212 swap, which got me excited about that option.
So... I picked up an LCT 208 clone off Ebay for $99, along with a generic TAV 30 series knockoff. I'm just getting started, but the components are coming together.
For most Predator-style conversions, builders are forced cut the downtubes off the donor frame in order to fabricate some sort of homebrew engine mount. I really hoped to avoid that, and it turns out I will barely be able to make it work. Rotating the position of the torque converter backing plate down to the lowest set of bolt holes shortens the overall length enough to allow the assembly to fit within the existing frame cradle. This leaves the engine pretty high in the engine bay, which looks weird, but in this case that's a good thing, since the engine is just high enough to clear the cross tubes at the front and middle of the frame. Other than chopping off a few extraneous tabs, I can leave the frame unmodified.
From the right side, the engine's sky-high placement looks pretty odd, but I am thinking I can utilize the space under the engine by integrating an electrical box into the engine mount and putting the battery under there. (My engine has an electric starter and I'm going to add a 60 watt alternator and lights eventually.) I grabbed an old Rebel 250 battery cover and slid it in just to get an idea how that might look.
The whole thing has to sit a bit further forward than I'd like, but if I moved it back, the frame would block both the intake and exhaust. As it is now, there is juuuust enough clearance on each side.
The downside is that the output sprocket is pretty far away from the swingarm pivot, which may play havoc with the chain clearance and tension. I don't know if it's necessary, but one idea to resolve this would be to run a narrow jackshaft with twin sprockets directly on swingarm pivot bolt, so that the chain geometry wouldn't change as the rear suspension moved. This arrangement would have the fringe benefit of allowing me some flexibility in the positioning the engine/CVT side-to-side in relation to the chain run to the rear wheel.
There's no way around it; this is going to be a weird bike, on multiple levels. Overall, however, I would say that all my random pieces continue to go together much more conveniently that I had any right to expect they would.
I said, I am a complete novice with this type of engine and lot of the specific details are pure voodoo to me — governors, splash lubrication, CVT tuning, parts interchangability, etc. — so I would welcome any help and assistance folks here can provide.
I have a fairly well-equipped shop, but its quite compact, and I recently found my parts shelves running out of space. So, I decided to take a pile of very random cast-off parts from various motorcycle projects and see how cheaply and easily I could build a bike out of them. For my framework, I bought a salvage frame from a '74 SST/Panther 175 Black Shadow for under $100 off Ebay. I started hanging parts off it with a vauge idea of building a street-legal gravel runner for exploring the flat, unpaved farm roads of rural Kansas.
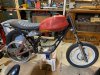
Originally, I was thinking that a Yamaha Blaster 200 motor would go nicely in this frame, but that turned out to be a more expensive proposition than I had expected. Meanwhile, a friend of mine recently helped build a KX/Predator 212 swap, which got me excited about that option.
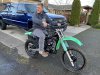
So... I picked up an LCT 208 clone off Ebay for $99, along with a generic TAV 30 series knockoff. I'm just getting started, but the components are coming together.
For most Predator-style conversions, builders are forced cut the downtubes off the donor frame in order to fabricate some sort of homebrew engine mount. I really hoped to avoid that, and it turns out I will barely be able to make it work. Rotating the position of the torque converter backing plate down to the lowest set of bolt holes shortens the overall length enough to allow the assembly to fit within the existing frame cradle. This leaves the engine pretty high in the engine bay, which looks weird, but in this case that's a good thing, since the engine is just high enough to clear the cross tubes at the front and middle of the frame. Other than chopping off a few extraneous tabs, I can leave the frame unmodified.
From the right side, the engine's sky-high placement looks pretty odd, but I am thinking I can utilize the space under the engine by integrating an electrical box into the engine mount and putting the battery under there. (My engine has an electric starter and I'm going to add a 60 watt alternator and lights eventually.) I grabbed an old Rebel 250 battery cover and slid it in just to get an idea how that might look.
The whole thing has to sit a bit further forward than I'd like, but if I moved it back, the frame would block both the intake and exhaust. As it is now, there is juuuust enough clearance on each side.
The downside is that the output sprocket is pretty far away from the swingarm pivot, which may play havoc with the chain clearance and tension. I don't know if it's necessary, but one idea to resolve this would be to run a narrow jackshaft with twin sprockets directly on swingarm pivot bolt, so that the chain geometry wouldn't change as the rear suspension moved. This arrangement would have the fringe benefit of allowing me some flexibility in the positioning the engine/CVT side-to-side in relation to the chain run to the rear wheel.
There's no way around it; this is going to be a weird bike, on multiple levels. Overall, however, I would say that all my random pieces continue to go together much more conveniently that I had any right to expect they would.
I said, I am a complete novice with this type of engine and lot of the specific details are pure voodoo to me — governors, splash lubrication, CVT tuning, parts interchangability, etc. — so I would welcome any help and assistance folks here can provide.