I'm working on the intake, and it's taking more effort than I expected.
I did find a commercially-available plug-and-play option, but it puts the carb so far outboard that I would have to run the cable outside of the tank, and I want to route the throttle cable through the tank tunnel in the conventional manner.
I tried a straight u-bend, but putting the carb close to the center of the frame also put the float bowl pretty close to the cylinder fins — really not ideal.
I slapped the 45° hose bend I had tried previously, and it moved the carb forward into a good position.
I verified that I will be able to get to the choke with the tank on.
So, there: desired configuration settled. But there's still a long way to go. The hose section will need to be replaced by an additional metal section; that silicone hose isn't fuel resistant, and even though it's molded, it allows the carb to sag a bit. But that's okay; I need to start fabrication again from scratch anyway. First of all, I was overconfident about my welding skills. After taking a great deal of time to fabricate a flange and fit it to the U-bend, I totally gobbed the welding.
Totally — as in, I'm too embarrassed to show any close-ups.
Secondly, one of the mounting screws for the exhaust is
right behind a frame tube. Installing and torquing it properly requires un-bolting the engine. It would be better to have the intake tract mounting bolts more accessible. The engine's intake is that odd D-shape, so I have an adapter flange to smoothly transition it to round (the red anodized plate visible in the photos). I'm going to make my own version of this adapter, similar to one that I made for my Honda CL125S:
- It will be thicker than the anodized one on there now (1/2" alloy) so the transition in shape of the interior hole will be less abrupt.
- It will have countersunk holes to mount to the intake, like above, and a second set of studs clocked to resolve the frame interference issue.
- The intake pipe mounting studs I'm adding will be slightly farther between centers. One of my problems welding was that there was very little clearance between the 1.25" tube and the bolt holes in the flange plate. The new studs will also be centered on the intake tube. The existing holes are offset slightly.
- The design is shaped so that I have three equidistant points at 120 degrees, so I can mount in my 3-jaw chuck to cut the taper in the center hole.
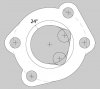