I recently picked up this mini bike frame for 30 bucks at a local motorcycle swap meet. It has issues, mainly the front fork is bent beyond repair. The main frame is straight but the kickstand is bent up, missing the scrub brake, the front fender mount missing, the rear one broken, and there is a large gouge in the tubing in one spot on the bottom of the frame (caused by a chain malfunction.) It is pretty messed up... possibly was involved in a mini crash.
The plan is to bring it back from the dead and maybe customize it slightly. I will have to use the old fork as a guide to fabricate a seemingly identical fork from scratch. I want to make the new handlebars a few inches taller to accommodate my height (6 foot) since the old handle bars touch my knees. It might be fun to add a rear seat shock absorber as well but I'm not sure about it yet. The scrub brake will be built from scratch. I'm going to weld in a repair section where the gouge is and straighten out the smaller stuff with heat. I will probably just paint it the frame when the times comes but may go the powder coat route. I'm going to mount a 1960's 3hp briggs on it and want to try to use a (probably chinese) mikuni carburetor paired with some sort of custom exhaust setup. I'm still trying to plan it out.
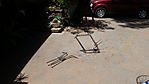
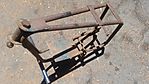
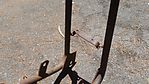
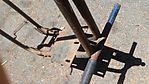
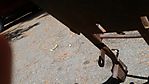
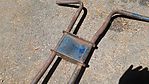
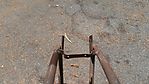
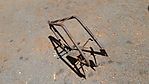
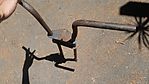
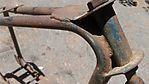
The plan is to bring it back from the dead and maybe customize it slightly. I will have to use the old fork as a guide to fabricate a seemingly identical fork from scratch. I want to make the new handlebars a few inches taller to accommodate my height (6 foot) since the old handle bars touch my knees. It might be fun to add a rear seat shock absorber as well but I'm not sure about it yet. The scrub brake will be built from scratch. I'm going to weld in a repair section where the gouge is and straighten out the smaller stuff with heat. I will probably just paint it the frame when the times comes but may go the powder coat route. I'm going to mount a 1960's 3hp briggs on it and want to try to use a (probably chinese) mikuni carburetor paired with some sort of custom exhaust setup. I'm still trying to plan it out.
Last edited: