I was cleaning out my photobucket and came across some pics of a old how to thread I did for the guy on a budget. I originally came up with idea when I was reading a thread about some unhappy results with a man painting some of his hardware black, So I went and threw this simple process togeather for him since then I have had alot of people use this method with good results so I figured I would share it here. The pics im using are with body bolts but can be used with any steel hardware.
You will need a few simple things, You will need a way to clean your hardware a blast cabinet, wire wheel or some way to clean off all the rust, muratic acid works well for stripping rust also, I might do something on that later...
Things you will need a propane torch some oil a small steel cup and pliers.
Then you need a rusty bolt
You will need a few simple things, You will need a way to clean your hardware a blast cabinet, wire wheel or some way to clean off all the rust, muratic acid works well for stripping rust also, I might do something on that later...
Things you will need a propane torch some oil a small steel cup and pliers.
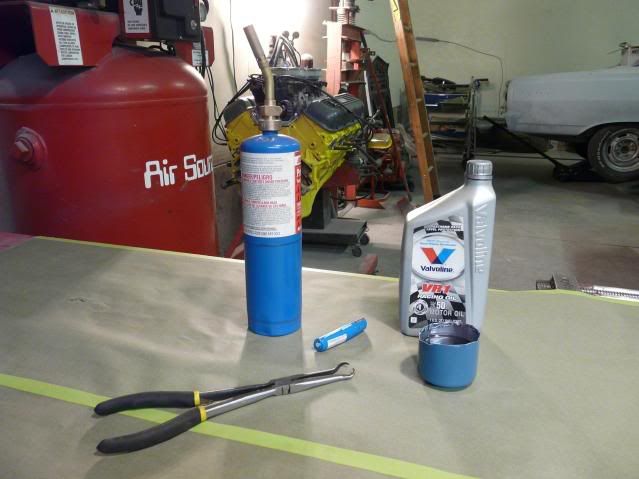
Then you need a rusty bolt
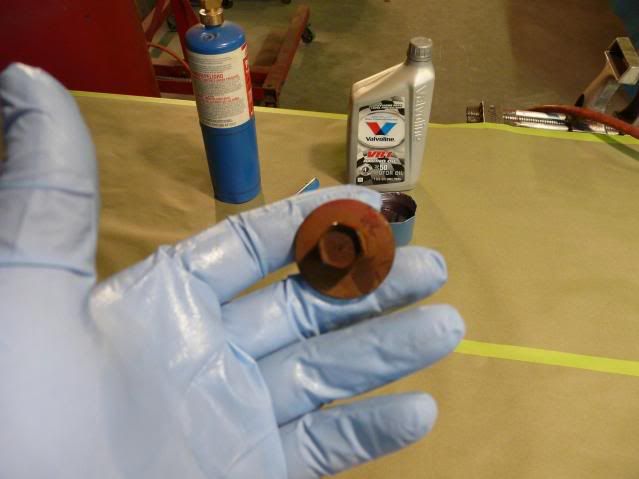