I hope this Gemini will work for the international class. I told my neighbor Maverick I was kicking around the idea of a minibike and he offered the perfect solution for my interests. It helps that my boy just turned 10 and has shown a growing interest in helping me out on the restorations. Yesterday Maverick dropped off a very nice Gemini and by dinner we had it torn apart. BTW it was 80F yesterday and the book is "A Christmas Carol".
I'm doing it the way my Dad started with me around that age. No power tools, the right tool for the right job, proper documentation, and I can still hear him yelling, "hold the flashlight where I can see it, not where you're looking!" Luckily, years of therapy worked and I can hold a flashlight now.
I'm doing it the way my Dad started with me around that age. No power tools, the right tool for the right job, proper documentation, and I can still hear him yelling, "hold the flashlight where I can see it, not where you're looking!" Luckily, years of therapy worked and I can hold a flashlight now.
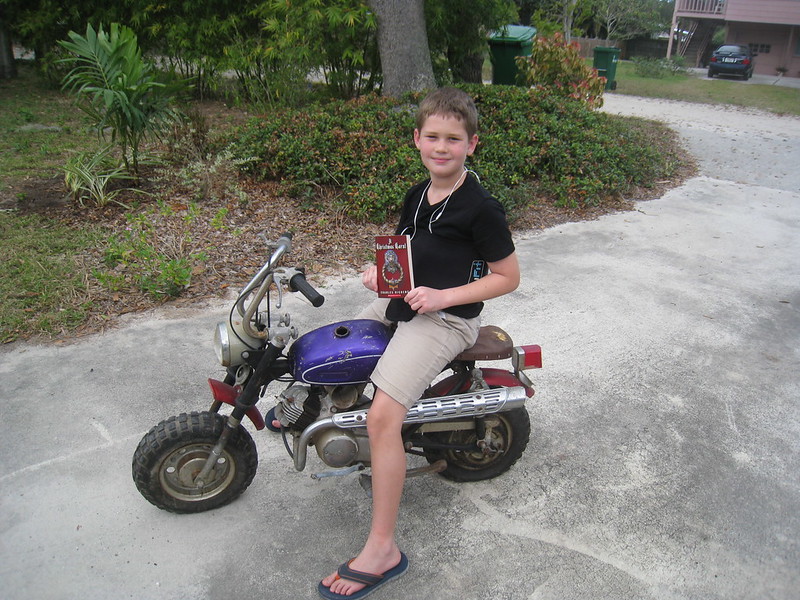
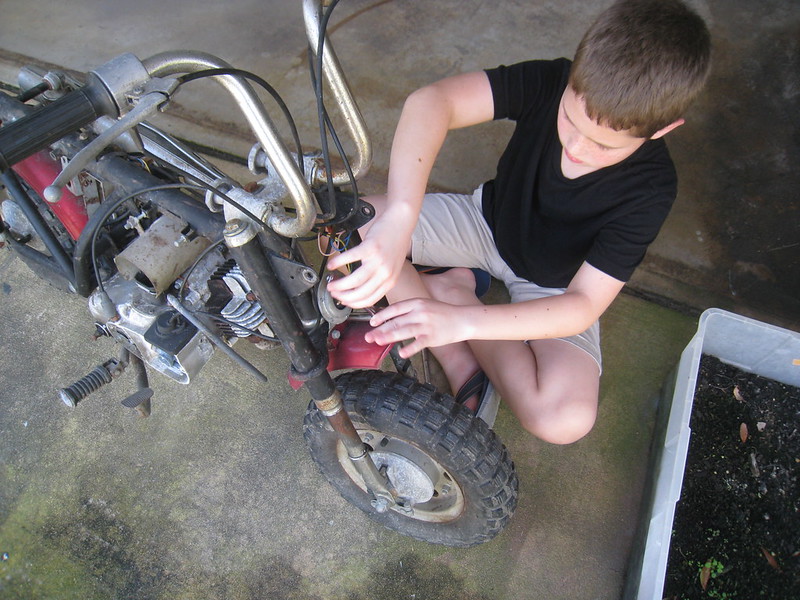