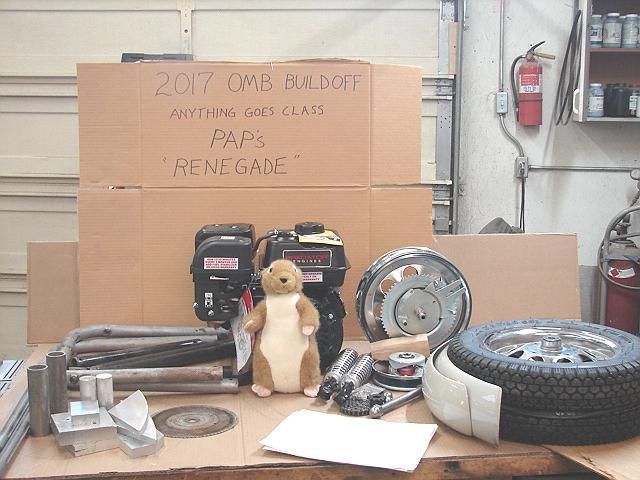
Anything goes class, scratch build. I'm attempting to make a bike about the size of a Rupp Roadster II. It will be suspended front and back, so I think I'm starting from the front and working my way to the back. There are still are a few parts that I haven't acquired yet, but I need to get more into the build to figure out what's gonna work. I'm Stoked!