Hi everyone,
I recently received a welder for Christmas, and was thinking of a project to build. I had a go cart as a kid, and loved it, and thought about building one of those, but we have ATVs and i kinda wanted something on two wheels.
After looking through quite a few build logs I stumbled onto Jeep2003's build log of a bike he made from an old swingset! I thought it was awesome. I now had a direction to go.
[/url]
I have been practicing with my welder just welding together random things I have laying around. (BTW - my welder is a Hobart Handler 125 wire feed welder with optional gas) I don't have gas yet, so I am using flux core wire. I have been very happy with the results, although I would like to eventually get the gas add-on kit and gas, but for now will just be using the flux-core.
I knew I was going to need a pipe bender, so I picked up one last thursday at Northern Tool (My Toy Store). On Thursday I also placed my order for the steel at the local metal supply place (which is not too local at 40 minutes away).
I tried out the bender on some 1" schedule 40 pipe that I had picked up and I was disappointed with the way the pipe would kink off on a 90 degree bend. I had read that packing the pipe with sand would help reduce this, and I watched a you tube video where the guy just duct taped the ends.
Friday I picked up my order at the metal supply place and this is what I got:
42 feet Schedule 40 3/4" pipe
4 feet Schedule 40 1" pipe
4 feet Schedule 40 1 1/4" pipe
4 feet Schedule 40 1 1/2" pipe
4 feet Schedule 40 1 3/4" pipe
4 feet 5/8" rod
4 feet 3/4" rod
4' x 6" x 1/4" plate
18" x 48" x 11ga sheet
Total was $157
I plan to build the majority out of 3/4" sch 40. Keep in mind that pipe is measured by the inside diameter so the pipe is actyally just over 1" OD.
I already had some 4" x 4' x 1/4" plate
I immediately set forth with bending the front forks when I got home Friday. I taped the end of one of a length of pipe, filled it to the top with sand and tapped it on the ground (concrete). The sand settled down and compacted. I topped it off with sand and tapped it again. After a couple more timed I taped the top with duct tape (3 layers).
Bending went much better and I got great results. Yes packing each pipe is a pain, but it is really worth it.
I wanted to keep the bike as low as practical, so I wanted to build the forks first. That way I could keep the body as low as I could make the steering neck.
I bent two pipes at 90 degrees, cut the 90 in the middle and spun the pipe around and welded it to make an "S" for the front forks.
I heated the bottom ends of the forks (after cutting to length) and used a hammer and anvil to flatten them out.
Next I cut the bottom tree out of the 4" wide 1/4" plate.
And welded it to the tubes. I calculated how wide I wanted the space for the front wheel, and cut a block of wood at that width. This is where I learned that jigs are good (as you will see later).
I recently received a welder for Christmas, and was thinking of a project to build. I had a go cart as a kid, and loved it, and thought about building one of those, but we have ATVs and i kinda wanted something on two wheels.
After looking through quite a few build logs I stumbled onto Jeep2003's build log of a bike he made from an old swingset! I thought it was awesome. I now had a direction to go.
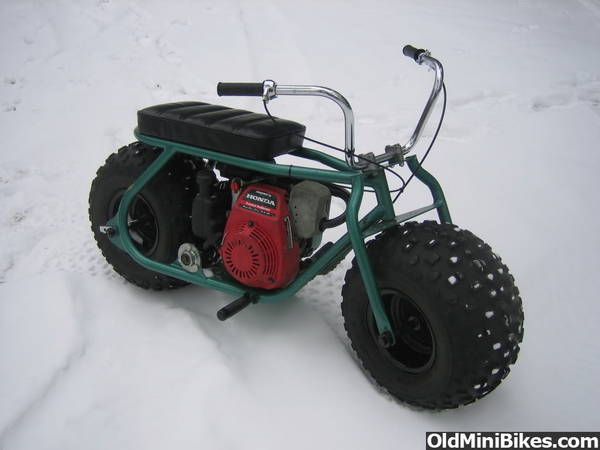
I have been practicing with my welder just welding together random things I have laying around. (BTW - my welder is a Hobart Handler 125 wire feed welder with optional gas) I don't have gas yet, so I am using flux core wire. I have been very happy with the results, although I would like to eventually get the gas add-on kit and gas, but for now will just be using the flux-core.
I knew I was going to need a pipe bender, so I picked up one last thursday at Northern Tool (My Toy Store). On Thursday I also placed my order for the steel at the local metal supply place (which is not too local at 40 minutes away).
I tried out the bender on some 1" schedule 40 pipe that I had picked up and I was disappointed with the way the pipe would kink off on a 90 degree bend. I had read that packing the pipe with sand would help reduce this, and I watched a you tube video where the guy just duct taped the ends.
Friday I picked up my order at the metal supply place and this is what I got:
42 feet Schedule 40 3/4" pipe
4 feet Schedule 40 1" pipe
4 feet Schedule 40 1 1/4" pipe
4 feet Schedule 40 1 1/2" pipe
4 feet Schedule 40 1 3/4" pipe
4 feet 5/8" rod
4 feet 3/4" rod
4' x 6" x 1/4" plate
18" x 48" x 11ga sheet
Total was $157
I plan to build the majority out of 3/4" sch 40. Keep in mind that pipe is measured by the inside diameter so the pipe is actyally just over 1" OD.
I already had some 4" x 4' x 1/4" plate
I immediately set forth with bending the front forks when I got home Friday. I taped the end of one of a length of pipe, filled it to the top with sand and tapped it on the ground (concrete). The sand settled down and compacted. I topped it off with sand and tapped it again. After a couple more timed I taped the top with duct tape (3 layers).
Bending went much better and I got great results. Yes packing each pipe is a pain, but it is really worth it.
I wanted to keep the bike as low as practical, so I wanted to build the forks first. That way I could keep the body as low as I could make the steering neck.
I bent two pipes at 90 degrees, cut the 90 in the middle and spun the pipe around and welded it to make an "S" for the front forks.
I heated the bottom ends of the forks (after cutting to length) and used a hammer and anvil to flatten them out.
Next I cut the bottom tree out of the 4" wide 1/4" plate.
And welded it to the tubes. I calculated how wide I wanted the space for the front wheel, and cut a block of wood at that width. This is where I learned that jigs are good (as you will see later).